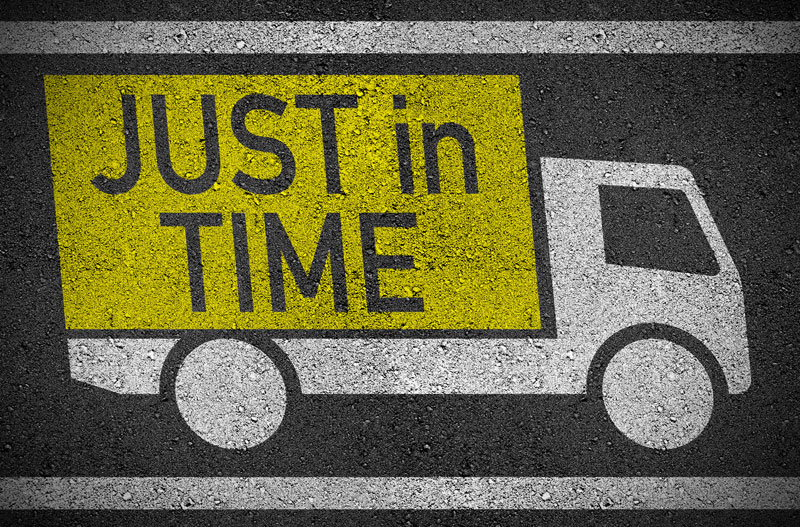
In the last couple of months, we have gone to grocery stores and pharmacies only to find empty shelves where the toilet paper, paper towels, antibiotics, cleaning supplies and hand sanitizer used to be.
Let’s take a moment to discuss supply chain as it applies to the retail industry. For non-perishable goods, canned foods and dry-goods, the only use of JIT in the retail sector is from the distribution center to the store location. From manufacturing to distribution centers, is traditional “push”, manufacturing utilizing highly sophisticated forecasting / demand planning, or just-in-case inventories. When digging deeper into the outages occurring today, the demand variability of these items is extremely low; meaning their demand is highly predictable. What we are experiencing is a once in a 100-year event! No demand planning / forecasting system is capable of predicting this type of event or crisis. If demand planning processes were able to forecast this event, I guarantee that this kind of knowledge would not be wasted on toilet paper and paper towels! Someone would be using that information to make billions in the stock market or to accurately predict weather patterns. Additionally, push systems are not flexible, responsive or agile enough to quickly pivot for sudden demand changes.
Read article